In the world of manufacturing, how long your injection molding machine Types
types last is key to making things efficiently and saving money. Ever thought about what makes some machines last longer than others? Let’s explore how the material, design, and upkeep affect how long your injection molds will last.
When making everyday items or complex parts, having the right injection molding machine Types is crucial. These machines, made of steel or aluminum, are the core of the process. They shape the plastic items we use every day. Knowing how long these molds last and what affects their life is vital for making things well and saving money.
Key Takeaways
- The lifespan of THY Precision injection molding machine types is influenced by a complex interplay of material, design, and maintenance.
- Proper maintenance and care can significantly extend the life expectancy of your injection molds.
- Choosing the right injection molding machine types for your specific needs is crucial for maximizing productivity and product quality.
- Understanding the average lifespan of injection molds is essential for effective production planning and cost management.
- THY Precision, a leading provider of high-quality injection molding machine types, can help you navigate the intricacies of mold selection and maintenance for optimal results.
Understanding Injection Molding Machine Types
In the world of injection molding, knowing the different types of machines is key for manufacturers. The hydraulic injection molding machine Types is one of the most common types. These machines use hydraulics to power the injection process. They are known for their reliability, versatility, and ability to work with many plastic materials and part sizes.
The type of injection molding machine Types used affects its lifespan and performance. Manufacturers need to think about material compatibility, part complexity, and how much they plan to produce. They should also consider the SPI mold classifications. These standards help categorize molds by their durability, material quality, and lifespan.
Hydraulic Injection Molding Machine Types
Many manufacturers choose hydraulic injection molding machines for their reliability and versatility. These machines use hydraulic fluid to power the injection process. This gives them precise control over molding. They can work with a wide range of plastic materials, from soft thermoplastics to strong engineering-grade polymers.
Feature | Hydraulic Injection Molding Machine Types |
---|---|
Power Source | Hydraulic fluid |
Precision Control | Excellent control over injection speed and pressure |
Material Compatibility | Wide range of plastic materials, including engineering-grade polymers |
Maintenance | Regular monitoring and servicing of hydraulic system required |
Hydraulic injection molding machine Types are popular because they are versatile and reliable. They help manufacturers meet a wide range of production needs and handle complex parts.

The Advantages of Electric Injection Molding Machines
In the fast-changing world of injection molding machine types, electric machines are changing the game. They bring many benefits that make them a top choice for manufacturers. These benefits include better efficiency, precision, and cost-effectiveness.
Electric injection molding machines are more energy efficient. They use electric motors for the injection and clamping parts. This means they use less energy than old hydraulic models. This leads to lower costs and a smaller environmental impact, which is good for eco-friendly businesses.
These machines also stand out for their precision and consistency. The electric drive system gives precise control. This means parts are made with tighter tolerances and more consistently. This is very important for industries like medical and aerospace that need very precise parts.
Electric injection molding machines are also cost-effective. They don’t need hydraulic fluid, which cuts down on maintenance costs. They are also more compact and use less energy. This means lower costs for setup and utilities, making them a smart choice.
“Electric injection molding machines are a big step forward in energy efficiency, precision, and cost-effectiveness. They are a great choice for modern manufacturing.”
The use of electric injection molding machines is expected to grow. This will give manufacturers a competitive edge. They will see better performance, less environmental harm, and more profit.
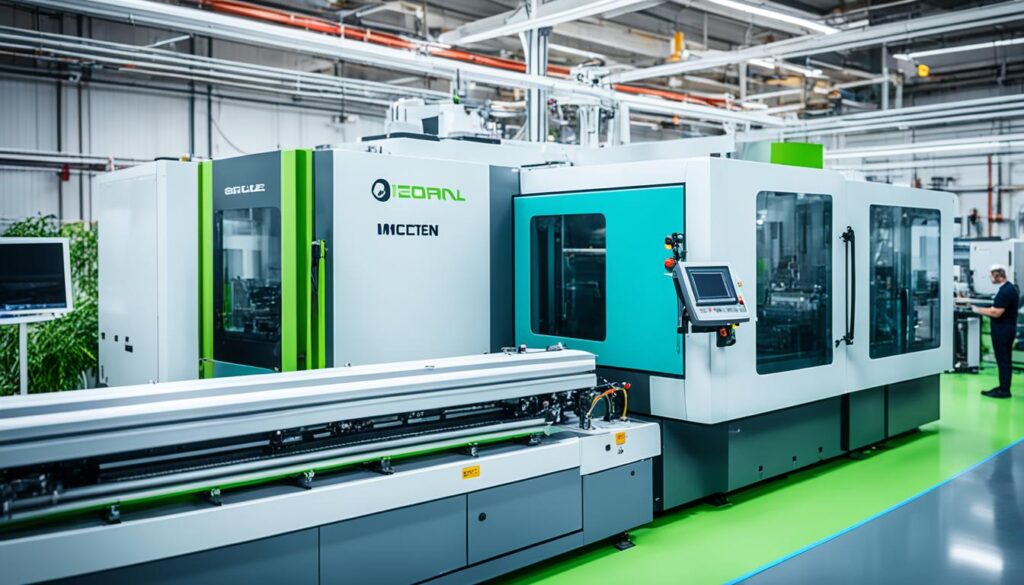
Hybrid Injection Molding Machines: The Best of Both Worlds
THY Precision offers a solution that combines hydraulic and electric technologies in one machine. This hybrid injection molding machine gives manufacturers top-notch performance, flexibility, and efficiency. It’s the best of both worlds in one package.
Vertical and Rotary Injection Molding Machines
THY Precision also has specialized machines for specific needs. Vertical machines are great for large or heavy parts, ensuring precise results. Rotary machines can make parts with multiple components or colors in one go.
These machines give manufacturers the flexibility they need for different projects. From big productions to custom parts, THY Precision’s machines help clients improve their performance, flexibility, and efficiency.
Machine Type | Key Features | Ideal Applications |
---|---|---|
Hybrid Injection Molding Machines |
|
|
Vertical Injection Molding Machines |
|
|
Rotary Injection Molding Machines |
|
|
At THY Precision, we know our clients have different needs. That’s why we offer a variety of injection molding machine types. Whether you need a hybrid, vertical, rotary, or a mix, our team is here to help you succeed.
“At THY Precision, we believe in empowering our clients with the most advanced and versatile injection molding solutions to help them stay ahead of the competition.”
Multi-Component and Insert Molding Machines
In the world of injection molding, two machines have changed the game: multi-component and insert molding machines. These machines are changing how we make complex parts. They offer flexibility and let us create parts with different materials.
Multi-Component Injection Molding: Combining Materials for Exceptional Results
Multi-component injection molding lets us inject different materials at once or one after the other in a single mold. This method, known as overmolding or co-injection, makes parts with different materials work together perfectly. It’s great for making parts that are strong, long-lasting, and perfect for certain jobs.
Insert Molding Machines: Integrating Pre-Formed Components
Insert molding machines take it up a notch by adding pre-made parts into the molding process. This makes a part that looks and works great, letting companies make unique and valuable products.
Looking to make your products better, prettier, or just more interesting? Multi-component and insert molding machines can help. With these technologies, THY Precision can help you make your injection molding better and create products that really stand out.
Feature | Multi-Component Injection Molding | Insert Molding Machines |
---|---|---|
Material Combination | Simultaneous or sequential injection of two or more materials | Incorporation of pre-formed inserts or components into the molding process |
Applications | Overmolding, co-injection, complex multi-material parts | Customized products with integrated components |
Benefits | Enhanced functionality, improved aesthetics, increased durability | Seamless integration of pre-formed inserts, versatile product design |
With multi-component and insert molding machines, THY Precision is ready to help you explore new possibilities in injection molding machine types. Let’s open up new paths for innovation and make products that really grab your customers’ attention.
Conclusion
The choice of injection molding machine types is key in today’s changing manufacturing world. It affects how long your machines last, how much they cost, and how flexible they are. You can pick from strong hydraulic machines, energy-saving electric ones, or versatile hybrid models to fit your needs.
Keeping your injection molding machine types in top shape is vital for making more and making more money. By regularly maintaining them, using the latest tech, and matching your production needs with the right machine types, you can make your equipment last longer and work better. This smart way of working makes your production cheaper and keeps your products reliable and high-quality.
Using the newest injection molding machine types brings more flexibility and versatility to your making process. If you need precise parts, complex items, or special insert molding, there are many new options out there. By keeping up with the latest in the field, you can pick the right injection molding machine types to grow your business and stay ahead in the market.